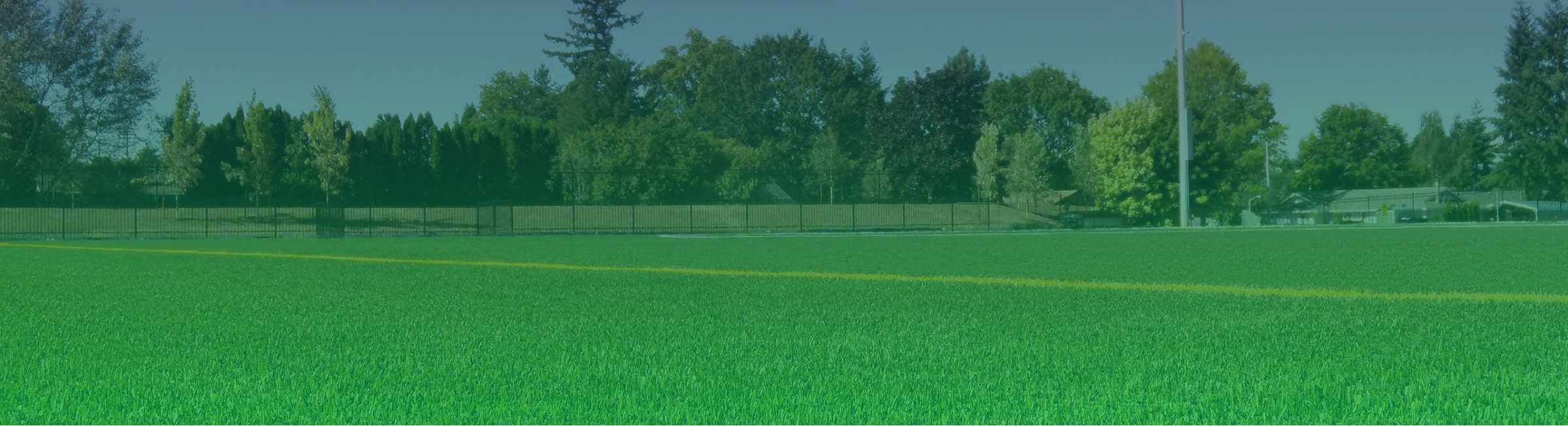
Most fields carry 8-year warranties, and hopefully, your field has outlasted its warranty.
When you’ve played and practiced on the same field day in and day out for years, it’s easy to get used to the declining appearance of an aging field. Some tell-tale visual signs that it might be time to replace your field include:
- Frequently loose inlays that pose tripping hazards and require repair
- Splitting and shedding turf fibers
- Tired field appearance, where the color of the field dulls to a grayish-green hue
- Lots of infill on the sides of the field (this can be improved with grooming and maintenance)
- Inlays and lines are significantly more worn than the turf in the body of the field
What’s more important than the appearance, of course, is the safety of your field. Over time infill migrates, displaces, and compacts (especially if it was initially installed with heavy sand content). Why does that matter? Because that means that there is less cushion between the athlete and the stone base underneath the turf (particularly if you didn’t buy a pad during the first installation). As players fall on the field, they are at a higher risk of concussion.
While you might be able to get by with a tired-looking field, you shouldn’t put your athletes at risk.
The only way to know for sure your field is unsafe is to have it tested. Call us today for a free field evaluation. We’ll provide a visual inspection and arrange for an independent shock absorbency test to be conducted.
If the field is found to have unsafe GMAX (shock absorption) levels, we can recommend steps to make your field playable until you can get your field fully replaced.
The main things to consider are:
You can keep it or let the turf company take care of the disposal. Most owners, let the turf company deal with it. After it has been removed it is usually repurposed into dog runs, batting cages, outdoor areas etc. The turf company factors in the replacement value with the removal/disposal costs. Sometimes it is disposed into a legal landfill but that is usually very expensive. Some owners choose to keep the old field. A word of caution though, it’s a lot of turf, even rolled up, and it’s heavy, cumbersome and occupies a large area on campus. Think long and hard before you decide to keep the field. It is usually better to grab a few rolls for your own use and let the turf company deal with the remainder
It’s totally up to you if you want to reuse your infill or buy new rubber and sand or an alternative infill. If you do elect to reuse your infill, it must be removed, cleaned, dried, and sieved to achieve proper specifications. It can be done, but only by an experienced company with specialized equipment.
The other option is to buy new infill. You can use the traditional SBR rubber and sand or you might consider some of the new infill options like the organics, TPE, EPDM, or Nike Grind. There are many options and many price points so it just comes down to a cost-benefit analysis for each owner.
The Subbase is critical because once the base is covered up with new turf it is very difficult to repair. The first question is have you had any drainage or puddling issues or are there any wavy lines or depressions on the field? These are telltale signs that there is a subbase issue. How is the condition of the perimeter wood nailer? Is it solid or showing signs of rot? If so, now is the time to replace the wood.
A better way to inspect the base, prior to removal, is to open up the turf and hire a professional soil company to take a few core borings to analyze the stone. They will find out what is in currently in place, does it drain, and does it have the proper depth? This will cost you about $1000-$2000 but it’s a critical report. The last option is to wait until the surface has been removed. At that point, we will have to inspect the field for drainage and planarity. If there are any soft spots or drainage issues, we will recommend a proper fix. You always need to allow for “fine grading” of the field with a laser equipped grader. It’s .15 to .20 psqf, and yields a perfect platform to accept the new turf. Since you cannot be 100 percent sure of anything prior to the turf removal, many of our customers use a subbase contingency of $20,000 to $50,000 in their budgeting and procurement. The beauty of this approach is that it builds in some money for repair, but if you don’t need it the contingency will be returned. Don’t worry, the fact is that most of the subbases we encounter have been properly installed and the remedial work is minimal.
Astroturf of course! We have several options to fit your needs. Our salesperson will look at your usage, your budget, and any special needs and determine the right AstroTurf product for you.
Plan on 30 to 45 days for the entire project. A major base issue could add a couple of weeks.
The following are budget building numbers that will help you get started in determining the cost of your project:
- .50 to $1.00 psqf for turf removal and disposal
- .15 to .20 fine grading the subbase
- $20,000 to $50,000 for a subbase contingency
- $4.00 to $6.00 psqf depending on turf type, inlays, prefab, infill type